Bringing XR into Manufacturing: Thoughts from Augmented World Expo ‘22
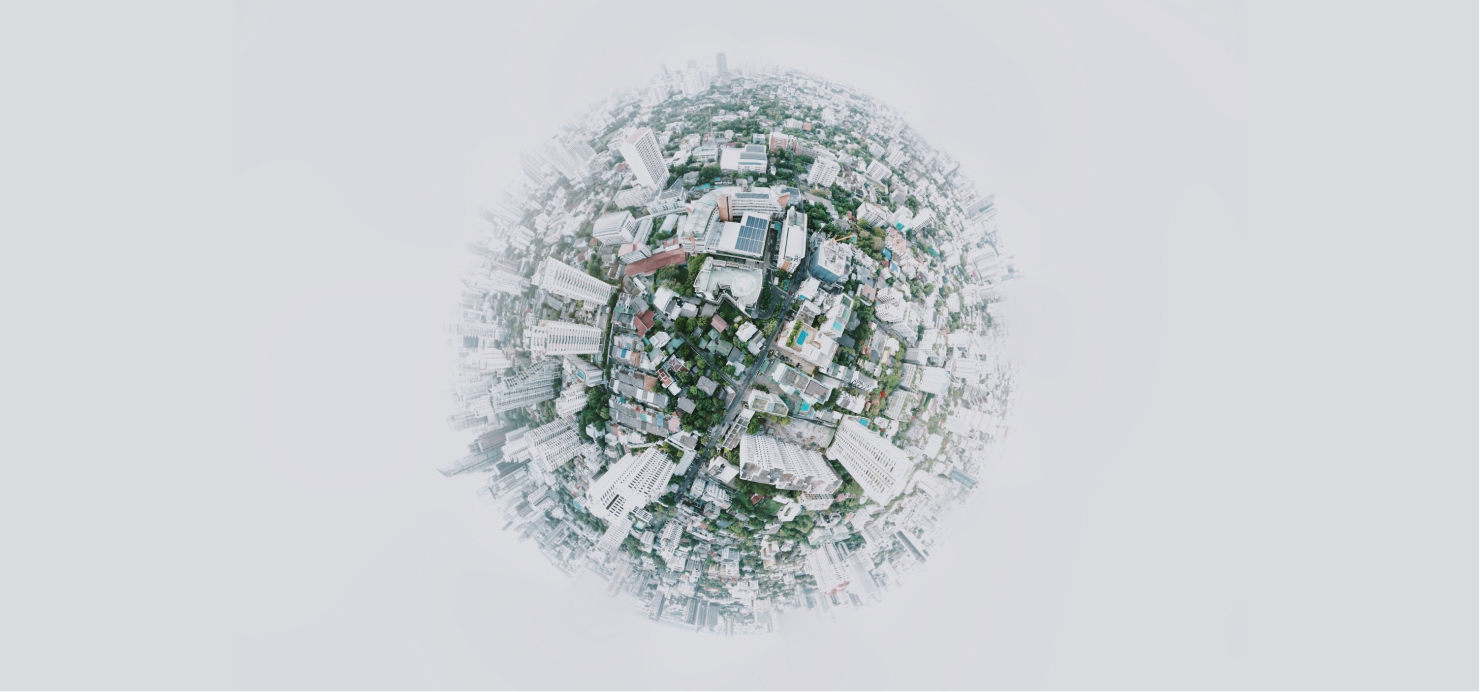
After wrapping up an exciting week at the Augmented World Expo we, the team here at Squint, are grateful to have had the opportunity to talk with AR / VR platform providers and hear from some companies in industry about how they’re applying these technology solutions to real problems in the real-world. We’re excited to share some of our findings with you! Let’s dive in.
You aren’t alone in your challenges
While listening to industry leaders at AWE, it was interesting to hear that from co-packing to the hospitality industry, many folks in management share the same problems:
(1) You have one shot to influence your operators: Operators make the product, and the worst thing management can do is disrupt their workflow and make them less productive by putting something that isn't ready or isn't effective in front of them. Put cleanly, new technology can’t be more complicated than the root problem the software is trying to solve in the first place.
(2) You’re searching for a way to boost operator engagement: turnover, new SKUs, re-training; no matter the need, it can be hard to capture the attention of operators and build a strong community at a facility.
(3) You’re looking for a way to standardize SOPs and audits: While initial training may be spot on, the phrase “use it or lose it” never fails to ring true. Unfortunately for management, this means that infrequent SOPs, safety materials, and audit checklists are easy to forget and are often replaced with word-of-mouth shortcuts.
(4) You’re looking for a solution that doesn’t require upfront time and knowledge investments: why does complex technology always have complex user experiences? Does one person in an office have to work for weeks to create a training plan or update a CAD model? In reality, why shouldn’t anyone be able to create training on-the-fly? Or even better, why can’t trusted operators, who know the procedures and machines best, create the training?
Now that we’ve discussed the challenges, the natural next question is “what can be done to solve them?” That’s where Squint comes in.
So, why is Squint publishing this blog?
Squint is an AR platform designed by manufacturers for manufacturing. Specifically, Squint empowers users and operators to perform spatial guided workflows on a handheld and share content spatially between the shifts on the factory floor.
Let’s address the challenges above, one-by-one.
(1) You have one shot to influence your operators
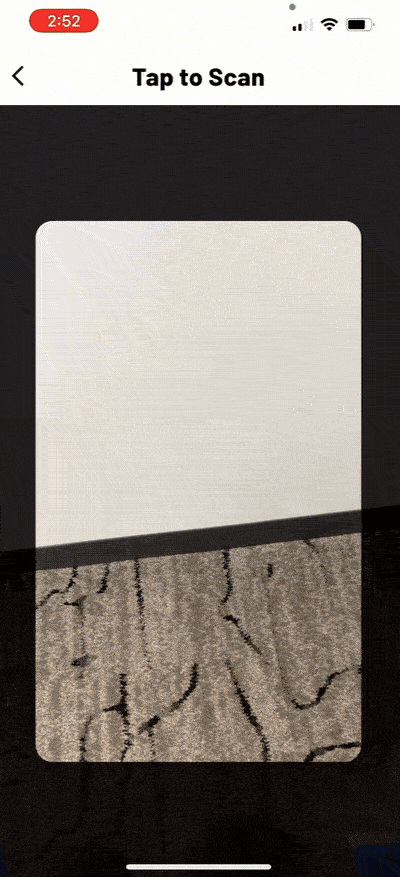
Squint is designed for operators. Our team seeks out and listens to operators, so we can solve their pain points without creating more problems.
One example of this user-forward methodology is the Squint approach to passwords.
Commonly, there are two methods a technology provider can take to provide login for their app. The first option is to ditch user profiles entirely, but this means that all of the valuable information on who’s doing what around a facility gets ditched too. The other option is to use passwords, however, we’ve learned that few operators are fans of having to remember passwords - you’re surprised, I know.
Now, instead of taking either of those common paths, we created a new method of logging into unique profiles using something that every operator uses: a badge. Now, Squint automatically recognizes your badge and logs you into your profile. It’s a bit of user-forward magic that makes securely signing in on the facility floor easier than ever.
(2) You’re searching for a way to boost operator engagement
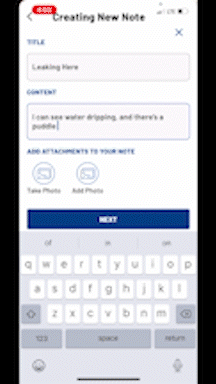
Anyone can create content in under a minute in Squint. We’re proud of this achievement as it positions Squint to get out of the way of the operator's actual work while still enabling them to quickly point out a leak, report a missing tool on your 5S board or share some of their tribal knowledge with the tap of a button.
Prior to Squint, operators had to leave their workstation to find a computer and create a ticket. The time and effort required to create a report often means only a portion of issues end up being reported.
In contrast, operators with Squint can type out text, take photos, and then pin all that content to a real world object - all from their phone or tablet!
(3) You’re looking for a way to standardize SOPs and audits
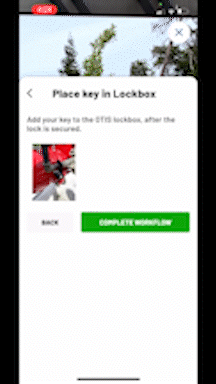
Whether your SOPs are digitized or held in 3-ring binders, it takes effort for operators to access those best practices. First, operators have to find the right binder, then they have to flip through it till they find the right knowledge. If SOPs are digitized, the same challenge stands in the way of operators, except this time they’re searching for a desktop workstation, trying to remember passwords and flipping through cluttered file systems. Either way, it’s easy to see why some operators might opt to go with their best recollection or ask a colleague rather than sourcing the standardized procedure.
With Squint, simply pointing a mobile device at a machine retrieves Workflows for relevant SOPs, safety materials, and audit checklists. When you click into a Workflow, Squint guides you through the steps, each with a spatial direction to specific points on the machine. Information is truly easy to access, meaning anyone can re-learn best practices on-the-fly without having to seek out and ask their supervisor.
(4) You’re looking for a solution that doesn’t require upfront time and knowledge investments
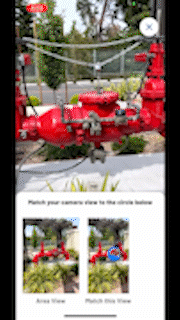
Many solutions in the AR space today resemble the Wizard of Oz. Sometimes this connotation comes from the awe of AR technology, and other times, because someone is emphatically telling you to focus on that awe without looking behind the curtains.
Squint is lightweight and supports a "build as you go" approach. Specifically, Squint requires nothing more than the app downloaded on your mobile device to get started. That’s right, no need to worry about fancy CAD models or printed QR codes. Overall, you can get started on Squint with very little effort and update as you progress through your journey.
TLDR, here’s the deal
We had the chance to speak with some amazing people at AWE, and we were particularly inspired when talking with leaders who are trying to bring XR into their facilities. We think they’re solving the hardest problem there is: bridging the gap between software and the real world. Updating the normal day-to-day practices of operators while dealing with the IT groups of a large company - it’s tough.
That’s why we, at Squint, are wrangling all of this new AR, VR, XR technology with the goal of uplifting, upskilling and elevating what people can do. We’re not trying to replace operators, we’re trying to empower them and that’s what we wake up every day inspired to do.
Want to talk through your challenges and see if Squint can help you? Book a Squint demo here