Why You Need to Collect Objective Evidence on the Factory Floor
.jpeg)
Objective Evidence: Qualitative or quantitative proof that an action (procedure, training, maintenance, etc) was completed. (e.g a timestamped photo of a completed Lockout/Tagout procedure)
If you're a manufacturing executive leading digital transformation, then you know that one of the most important things you can do is collect objective evidence on the factory floor. Doing so can help you identify improvements that need to be made, track progress, and make sure that your employees are working safely and efficiently. Here are just a few of the reasons why you should be collecting objective evidence on the factory floor…
It Helps You Identify Problems
One of the main reasons why you should be collecting objective evidence on the factory floor is because it helps you identify problems. Maybe there's a machine that keeps breaking down, or maybe there's a process that isn't as efficient as it could be. Whatever the problem may be, it's likely that objective evidence will help you identify it so that you can find a solution.
It Helps You Track Progress
Another reason to collect objective evidence on the factory floor is because it helps you track progress. Let's say you're trying to improve safety in your factory. By collecting objective evidence, you can track whether or not accidents are becoming less common over time. This type of data is invaluable when it comes to demonstrating the effectiveness of your efforts.
It Helps You Make Sure Employees Are Working Safely
Finally, collecting objective evidence on the factory floor can help you ensure that your employees are working safely. This is especially important if you have employees who are working with hazardous materials or operating dangerous machinery. By collecting data on things like near-misses and accidents, you can get a better sense of which areas need improvement when it comes to safety.
Collect Objective Evidence Automatically With Squint
If you're not already collecting objective evidence on the factory floor, now is the time to start. Doing so will help you identify problems, track progress, and ensure that your employees are working safely.
Squint is a powerful new technology solution that helps manufacturers do just that. Squint Procedures give you the ability to digitize your procedures and work instructions with ease. You can then incorporate Squint Forms into Squint Procedures directly, meaning you can add a form to any step of a procedure.
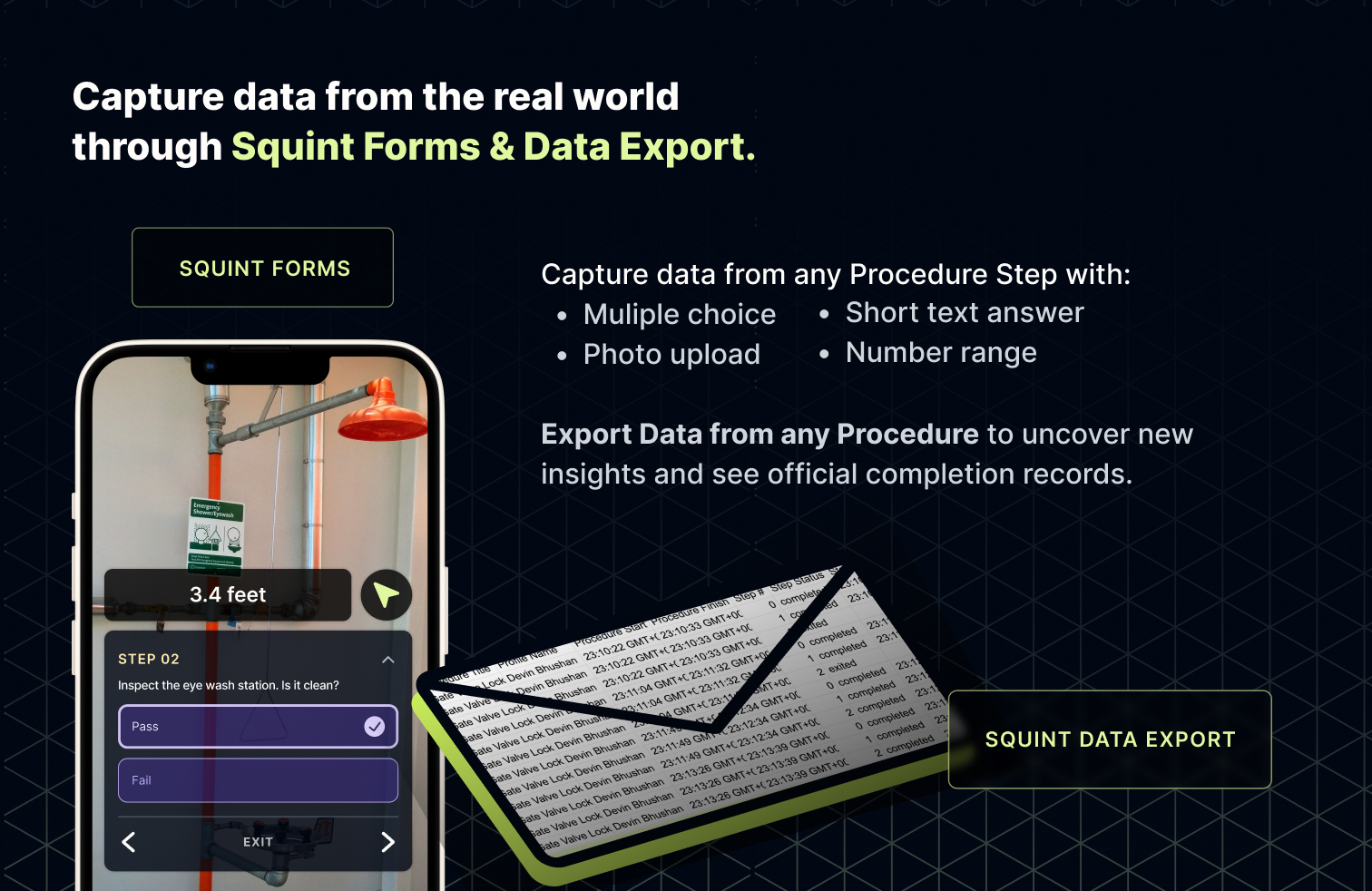
Then, when the procedure is run, the operator will automatically be prompted to engage and submit data. This objective evidence can be exported and analyzed as part of your continuous improvement efforts. With the tap of a button, a neatly packaged CSV shows up in your inbox containing: operator name, time and date, answers to any included forms, and rich data on runtime and completion status of the procedure. Objective evidence like this is crucial for improving processes and making informed decisions about process changes. With Squint, you can collect this objective evidence easily and efficiently.
To learn more about Squint or to get started, book a 30-minute demo.